Description
Static Inline Mixers
In all Series Static Mixers, a helical mixing element directs the flow of material radially toward the pipe walls and back to the center. Additional velocity reversal and flow division results from combining alternating right- and left-hand elements, thus increasing mixing efficiency. All material is continuously and completely mixed, eliminating radial gradients in temperature, velocity and material composition.
Numerous independent studies have shown that Static Mixers maximize mixing efficiency without the wasted energy and material blockage typically found in more restrictive motionless mixers.
How Does A Static Mixer Work?
The mixing elements or fins induce turbulent flow in the mixer housing which mixes chemicals added either ahead of the mixer or through an injection port on the mixer housing. The process media will be mixed 95% within 3D (pipe diameter) of the mixer outlet, this is called the COV or Coefficient of Variation.
Static mixers are aimed at 0.5 or 95% mixing at 3D (pipe diameter) of the mixer outlet.
There is no typical static mixer design, a variety of designs are available to suit specific applications.
Helical coil mixers for the chemical pharmaceutical and food industries.
Fin mixers for the water industry - Fin mixers. The mixing elements (foils) of the mixer are mounted on the walls of the mixer housing and are so-called open designs, which means that they are less likely to clog, then the pressure drop is lower than that of a helical coil mixer.
SK Series Model
Model |
Dg(mm) |
dh(mm) |
Q(m3/h) |
SK-5/10 |
10 |
5 |
0.15-0.3 |
SK-7.5/15 |
15 |
7.5 |
0.3-0.6 |
SK-10/20 |
20 |
10 |
0.6-1.2 |
SK-12.5/25 |
25 |
12.5 |
0.9-1.8 |
SK-16/32 |
32 |
16 |
1.4-3.2 |
SK-20/40 |
40 |
20 |
2.2-4.5 |
SK-25/50 |
50 |
25 |
3.5-7.0 |
SK-32.5/65 |
65 |
32.5 |
5.9-12 |
SK-40/80 |
80 |
40 |
9-18 |
SK-50/100 |
100 |
100 |
14-28 |
SK-62.5/125 |
125 |
125 |
22-44 |
SK-75/150 |
150 |
150 |
31-64 |
SK-100/200 |
200 |
200 |
56-110 |
SK-125/250 |
250 |
250 |
88-177 |
SK-150/300 |
300 |
300 |
127-255 |
SK-175/350 |
350 |
350 |
173-346 |
SK-200/400 |
400 |
400 |
226-452 |
SK-250/500 |
500 |
500 |
353-706 |
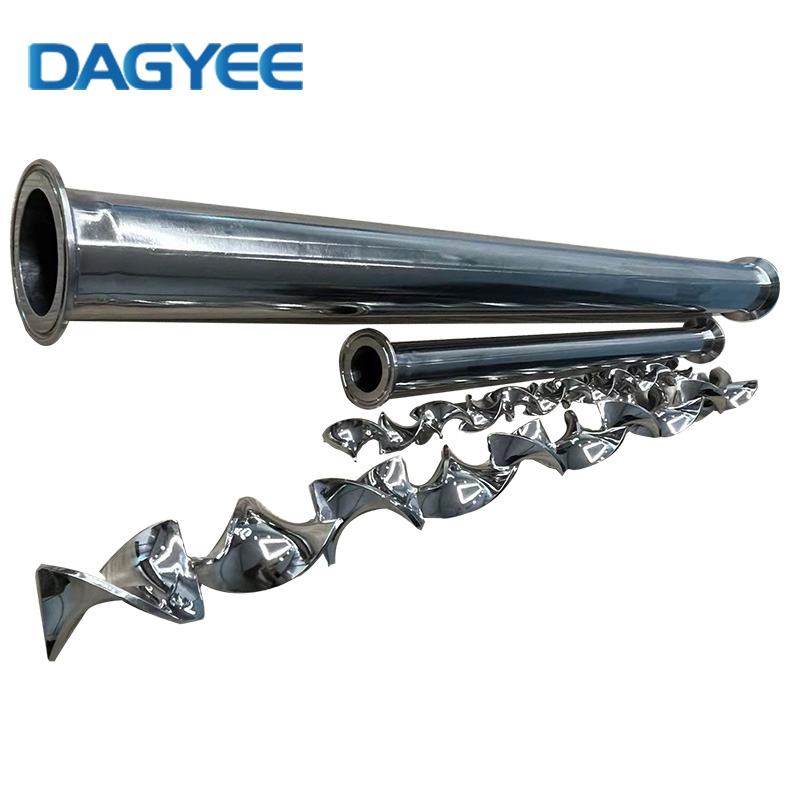
Benefits of Static Mixer
Maintenance-Free
Static Mixers are built to last using industrial grade materials specifically tailored to your application.
Low-Cost
Static Mixers are a low-cost alternative to traditional tank mixers both at purchase and during the mixer's lifetime. There are no running costs associated with operating Static Mixer on top of running your existing pipeline.
Low Energy Requirements
Because static mixers are motionless by design, all the energy required to provide a perfect blend is provided by the energy of the flow stream.
No Moving Parts
Unlike traditional mixers, static mixers remain motionless during the mixing process.
Custom-Designed for Your Application
Static mixers can be custom-tailored to fit your requirements.
Quick Delivery
Maintains complete control over its production process. All static mixers are built in-house at Koflo's manufacturing facility outside Chicago and can be manufactured to meet your project schedule.
Mixing Applications
Turbulent Blending
The Static Mixer produces rapid mixing by inducing circular patterns that reverse direction at each element intersection.
Laminar Blending
The alternating helical elements of the Static Mixer continually divide, stretch and reorient the flow stream to produce complete mixing with minimum pressure drop.
Liquid/Liquid Dispersion
The uniform turbulent shear field of the Static Mixer quickly disperses immiscible liquids and produces a narrow drop size distribution.
Gas Liquid Dispersion
Gases can be incorporated into turbulent liquids using the Static Mixer. Mass transfer rates are dramatically enhanced to maximize absorption or reaction.